
10 March, 2024
Unveiling the Artistry of 3D Modeling and Reverse Engineering
In the realm of modern design and engineering, two indispensable techniques stand tall: 3D modeling and reverse engineering. Together, they form a dynamic duo, enabling innovation, problem-solving, and creative expression across various industries. F...
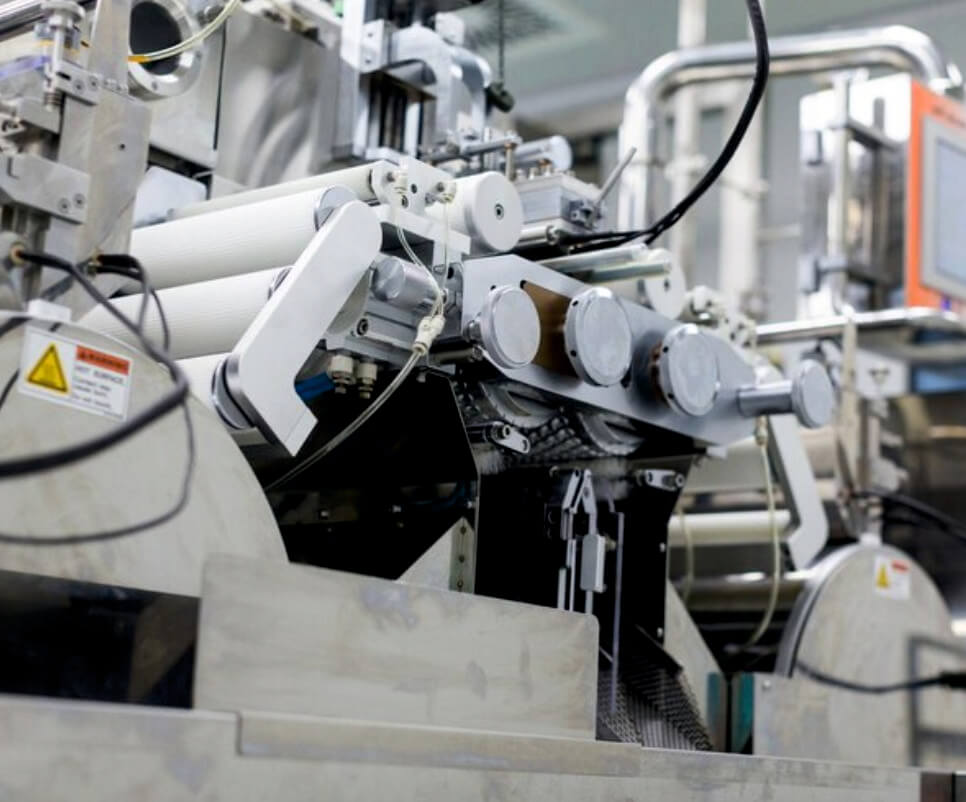
06 March, 2024
The Ingenious World of Injection Moulding: Crafting Tomorrow's Innovations
In a world where precision, efficiency, and creativity converge, injection moulding stands as a cornerstone of modern manufacturing. From the smallest components in our everyday devices to the intricate parts of automotive engineering, this ingenious...
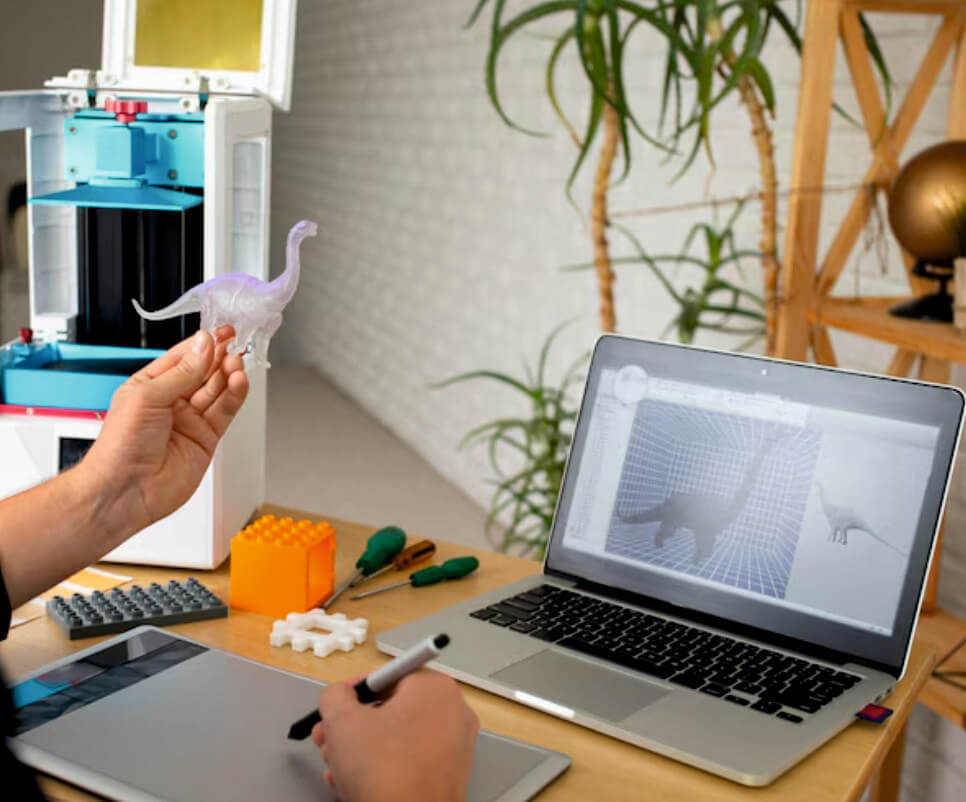
03 March, 2024
Unlocking Innovation: Exploring the Wonders of 3D Printing
In the realm of manufacturing and prototyping, few technologies have sparked as much excitement and innovation as 3D printing. Often referred to as additive manufacturing, 3D printing has transcended its origins as a niche technology to become a tran...