The Ingenious World of Injection Moulding: Crafting Tomorrow's Innovations
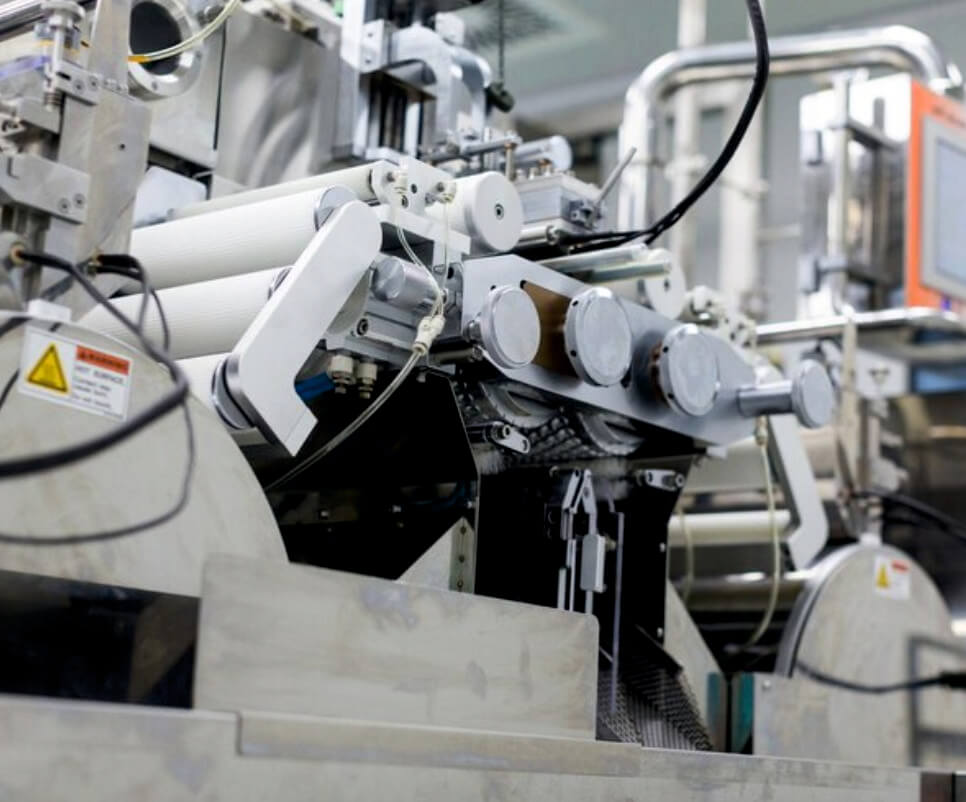
In a world where precision, efficiency, and creativity converge, injection moulding stands as a cornerstone of modern manufacturing. From the smallest components in our everyday devices to the intricate parts of automotive engineering, this ingenious process quietly shapes the fabric of our technological landscape. Let's delve into the fascinating realm of injection moulding and explore how it's revolutionizing industries worldwide.
Unveiling the Process: At its core, injection moulding is a manufacturing process used to produce parts by injecting molten material into a mould. This molten material, typically thermoplastics or thermosetting polymers, is injected under high pressure into a mould cavity, where it cools and solidifies to take the shape of the mould. Once solidified, the part is ejected, ready to be used in various applications.
Precision Engineering: One of the most remarkable aspects of injection moulding is its ability to produce intricate and complex parts with unparalleled precision. The process allows for tight tolerances and consistency, ensuring that each part meets the exact specifications required. This level of precision is crucial in industries such as aerospace, medical, and electronics, where even the slightest deviation can have significant consequences.
Versatility in Material Selection: Injection moulding offers a vast array of material options, ranging from commodity plastics to high-performance polymers. This versatility allows manufacturers to choose materials that meet specific requirements such as strength, durability, heat resistance, and chemical compatibility. Whether it's ABS, polycarbonate, nylon, or polypropylene, there's a material suited for every application, making injection moulding an incredibly adaptable manufacturing solution.
Efficiency Redefined: Efficiency lies at the heart of injection moulding, with its ability to produce large volumes of parts rapidly and cost-effectively. Once the mould is set up, the production process becomes highly automated, minimizing labor costs and maximizing output. Furthermore, the repeatability of the process ensures consistent quality across mass-produced parts, reducing waste and optimizing resource utilization.
Driving Innovation: Injection moulding serves as a catalyst for innovation, enabling designers and engineers to push the boundaries of what's possible. Its ability to produce complex geometries and intricate designs unlocks new opportunities for product development and functionality. From lightweight components in automotive engineering to miniaturized electronics and medical devices, injection moulding plays a pivotal role in bringing innovative ideas to life.
Sustainability in Focus: In recent years, there has been a growing emphasis on sustainability within the manufacturing industry, and injection moulding is no exception. Manufacturers are increasingly exploring eco-friendly materials, optimizing processes to reduce energy consumption, and implementing recycling initiatives to minimize waste. With advancements in bioplastics and recycled materials, injection moulding is evolving towards a more sustainable future, where efficiency and environmental responsibility go hand in hand.
Conclusion: In the ever-evolving landscape of manufacturing, injection moulding stands as a testament to human ingenuity and innovation. Its precision, versatility, efficiency, and sustainability make it indispensable across a multitude of industries, shaping the products we use every day and driving technological advancements forward. As we continue to push the boundaries of what's possible, injection moulding will undoubtedly remain at the forefront of manufacturing excellence, shaping tomorrow's innovations one mould at a time.